A Hybrid Approach to Manufacturing
Blending industry expertise with cutting-edge in-house technology development, Terran R leverages additive manufacturing alongside traditional processes to deliver a high-performance, cost-effective vehicle. For components that benefit from rigorous hardware testing, additive manufacturing enables rapid iteration cycles. For larger, longer-lead time structures where key learning can happen through simulation, we utilize traditional manufacturing methods. This hybrid approach optimizes for rapid development and scalability, ensuring we can bring Terran R to market quickly for our customers.
The Best of Additive & Next-Gen Tech
Innovate. Iterate. Elevate.
For elements of Terran R where rapid iteration is key, we prioritize nimble manufacturing methods. The Aeon R engines integrate powder bed fusion (PBF) with proprietary wire arc additive manufacturing (WAAM) techniques to shorten the design, build, test lifecycle without compromising on performance. Beyond faster iterative cycles, additive manufacturing also enables production of lighter, stronger, and more efficient components.
PBF: Precision & Performance
Relativity produces high-performance engine components with unmatched precision and efficiency. Powder bed fusion (PBF) printing allows for the creation of intricate internal geometries, such as cooling channels and fluid passages, with reduced mass and enhanced durability – critical factors in building high-performance rocket engines.
Mass & Cost Efficiency – By using additive rather than subtractive manufacturing, parts are produced with only the material needed.
Complex Design Capability – 3D printing enables integrated design of intricate cooling channels and fluid passages, optimizing performance.
Rapid Iteration In Practice – The team completed 14 design-print-test cycles for the main injector in just three months, significantly accelerating innovation.
WAAM: Strength & Scalability
Relativity’s proprietary wire-arc additive manufacturing (WAAM) platform enables seamless integration of multiple materials and freeform structures within a single manufacturing cell. By applying WAAM cladding atop a PBF-printed main combustion chamber, optimization of mixed-material use can be achieved. This technology has evolved into a high-volume production solution for Aeon R engines.
Material Versatility – Combines copper-based alloys for thermal properties and nickel-based alloys for structural integrity.
Integrated Manufacturing – Enables cladding alongside the creation of freeform features such as flanges and bossports, in a single production step.
Scalability – Transitioned from a development project to an automated production process, improving efficiency at scale.
Optimizing Large-Scale Manufacturing
For long-lead components such as primary structures, Terran R utilizes industry-proven, highly-scalable techniques, with proprietary innovations to enhance performance. This large-scale hardware is amenable to analysis, so learnings can be integrated before production. Rapid, scalable production is enabled by in-house manufacturing centers, alongside the support of trusted suppliers.
Smart Manufacturing, Accelerated Results
From precision welding to high-efficiency CNC machining, every process at Relativity is optimized for speed, scalability, and cost. Our production system in Long Beach, CA integrates best-in-class machinery alongside proprietary software and automated tooling to uplevel production for Terran R.
Panel Routing – Removes 60% of panel weight, optimizing structural efficiency and enabling intricate geometries for tank and thrust structure production.
Vertical Friction Stir Welding – Proprietary tooling enables fast, adaptable welds for panels and stiffeners, allowing us to quickly unlock process adjustments.
Circumferential Friction Stir Welding – Self-reacting friction stir welding reduces complex tooling needs, while mobile track welding increases efficiency, ensuring precise, scalable production.
CNC Machining – Utilizes CNC work centers, vertical turning lathes, and multi-axis propulsion CNC machines to mill and machine Terran R primary structures, propulsion components, and large flight parts with speed and precision.
A Platform for the Future
Relativity is building an end-to-end additive manufacturing system integrating robotics, controls software, and advanced simulation tools to manufacture large-scale metal structures. Collaborating across disciplines, the team is developing a unified platform for additive manufacturing, in-situ monitoring, and inspection within a single print cell. These innovations are progressing in parallel to Terran R development, with the goal to transform the industrial base.
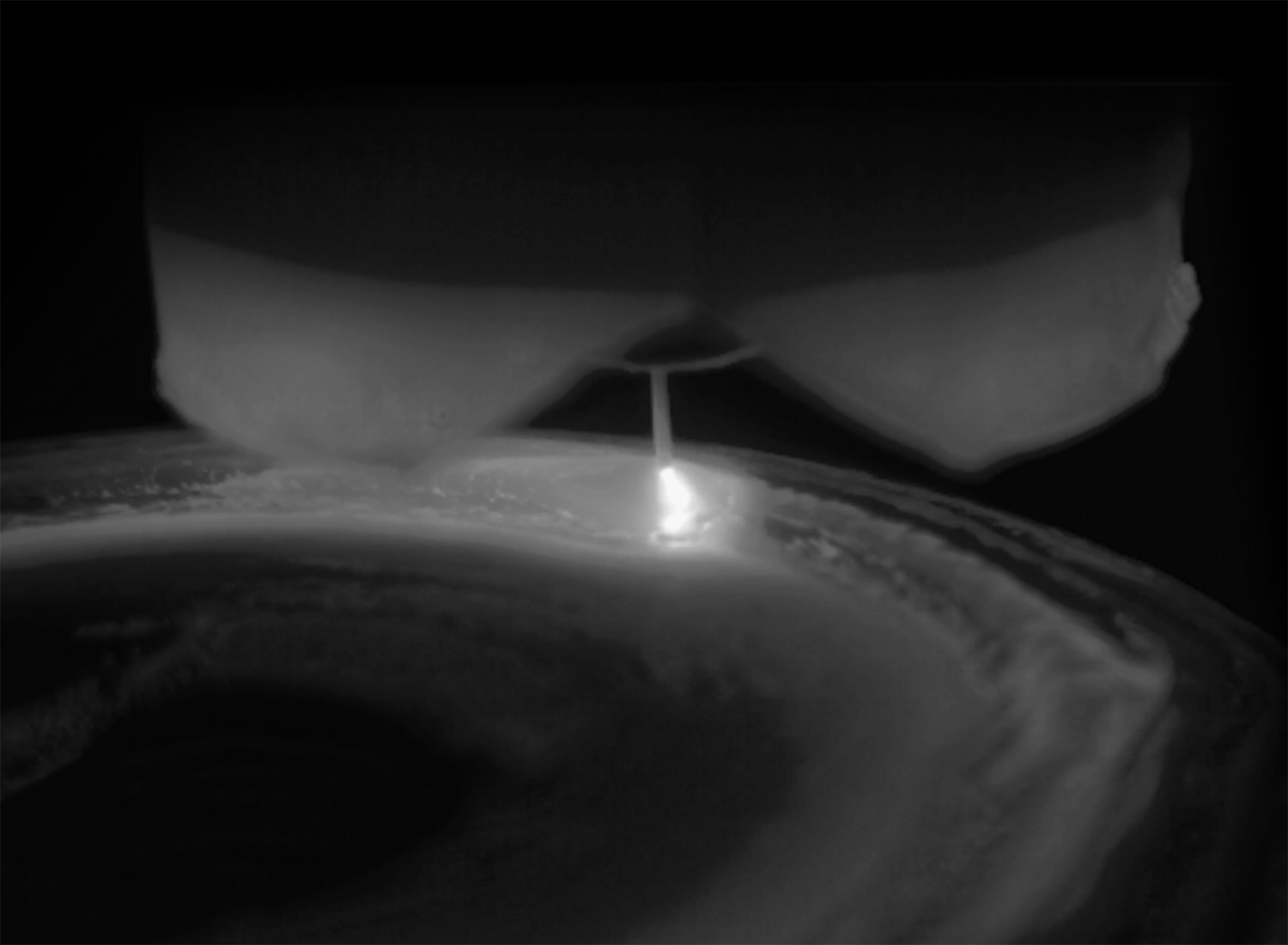
AI Controls:
Real time quality control and part inspection
Proprietary software enables real-time observation, analysis, and control of the additive manufacturing process, monitoring porosity, distortion, and overall quality layer by layer.
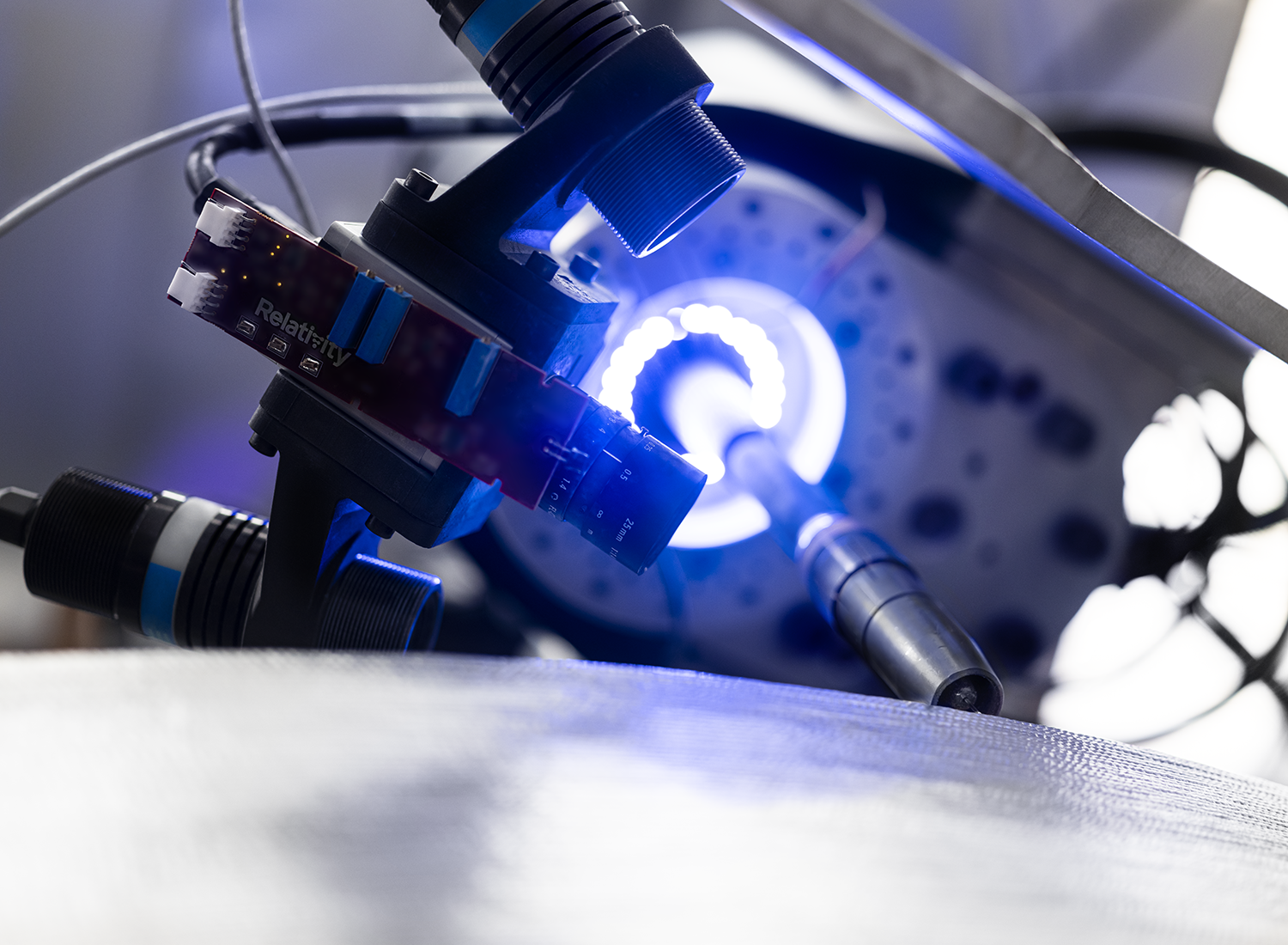
Machine Learning:
Optimizing Performance
Advanced algorithms coordinate systems to enhance the speed, quality, and efficiency of large-scale additive manufacturing.
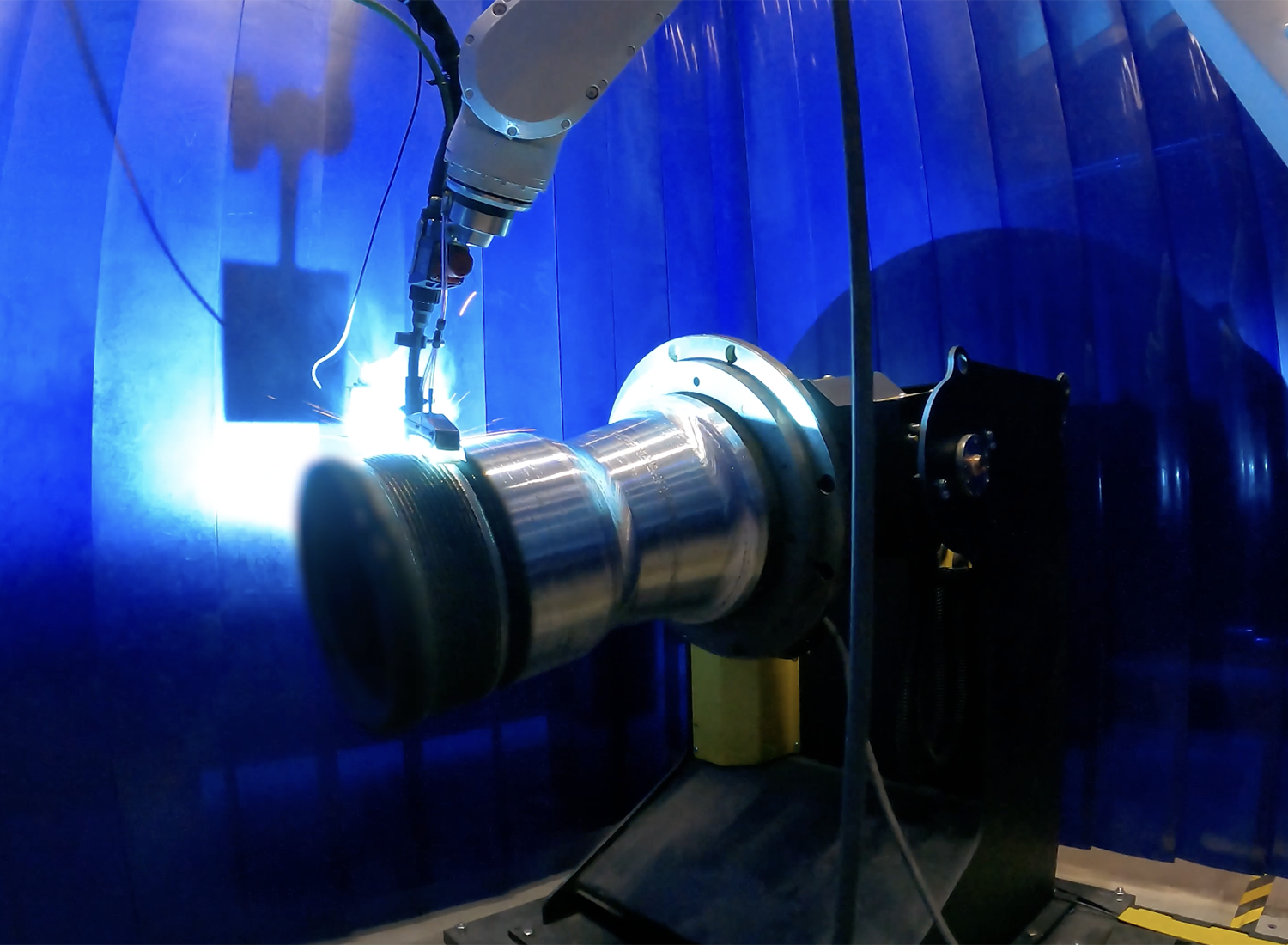
Robotics:
Integrated Motion Control
An in-house robotics control platform consolidates multiple interfaces, enabling real-time motion control across robots and supporting equipment within a unified system.
Advanced Materials, Proven Expertise
Relativity’s world-class team leverages advanced material science to drive aerospace innovation. Their expertise spans from novel alloy development to fracture and fatigue analysis – all supported by in-house testing capabilities. This foundation powers the development of Terran R, a highly reusable, next-generation launch vehicle.
Advanced Thermal Protection System: In-house development and testing drives innovation in cutting-edge reusable heat shields. Relativity’s proprietary thermal protection system is undergoing material testing for durability, mass efficiency, and thermal performance.
High-Performance Propulsion: Aeon R engines utilize the GRCop-42 alloy, co-developed by NASA. Its high-strength nickel optimizes thermal and structural integrity, withstanding extreme temperatures up to 6,500°F.
Optimized Structural Materials: Terran R’s primary structures are built from high-strength aluminum alloys, enhanced by friction stir welding and validated through NDE inspection for maximum durability and efficiency.